
Closed-Loop Subsonic Wind Tunnel
Nielsen-Kellerman's ongoing efforts to improve measurement accuracy and certification for our products led the mechatronics team to begin the specifications and design of a subsonic wind tunnel. As the lead for this project, I was in charge of the initial research, design, and construction of this tunnel.
​​​
Test section's cross-section:16 in x 16 in
Max speed: 10 m/s ​
Contraction ratio: 6:1
Footprint: 4 ft x 7 ft x 18 ft
​
Initial Design


(A)

The screenshots (A, B, & C) are updated SolidWorks design after deciding on the material and process to construct the tunnel.
(B)

The test section design was also completed.
(C)

The last item to sort out is the desired measurement tool besides a standard anemometer.
The construction of the aluminum support frame and wooden tunnel sections completed

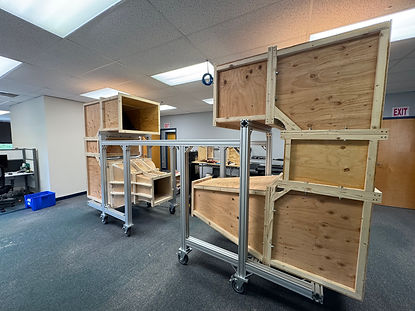
Moments during construction
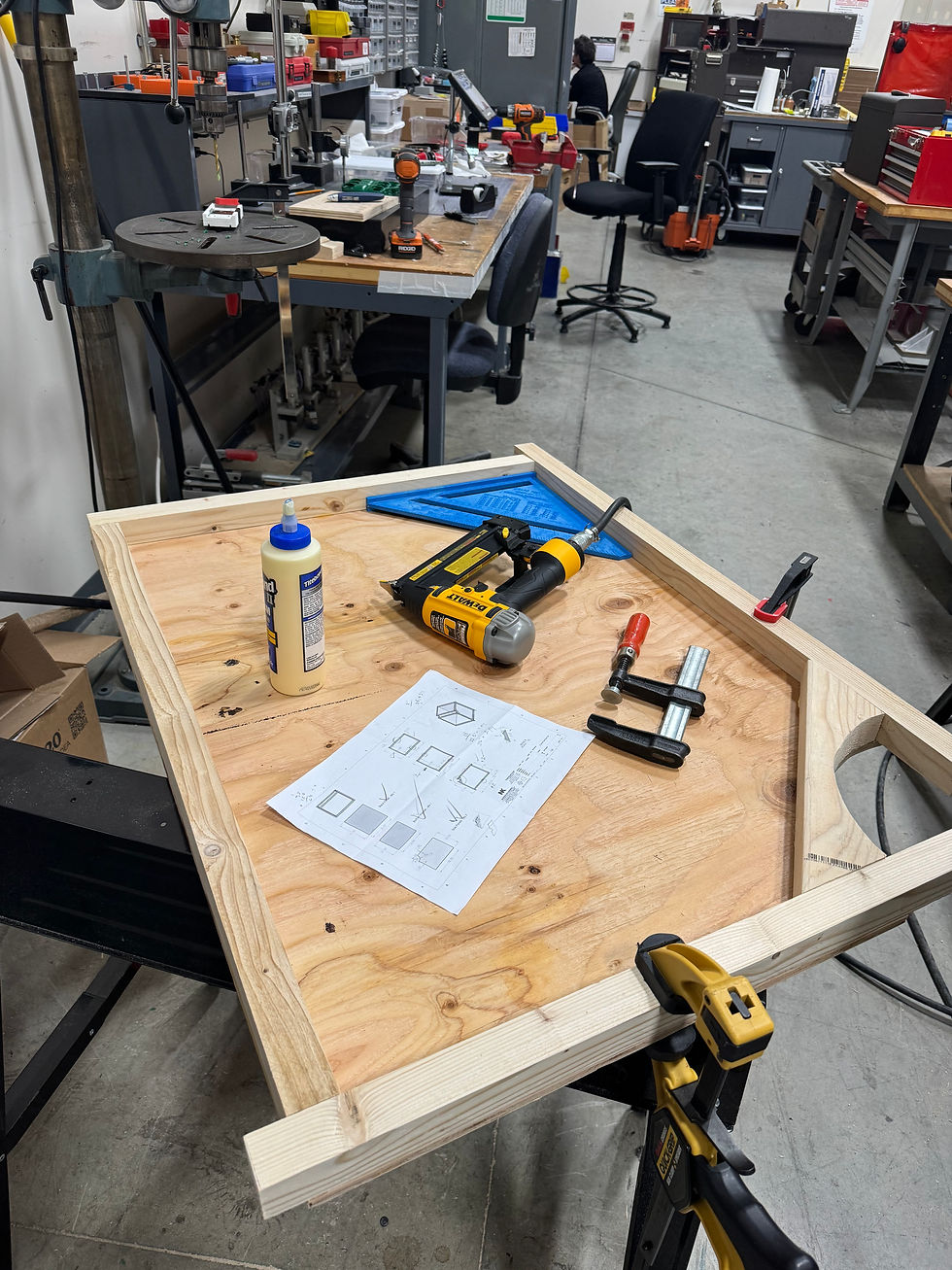
Squaring 101

Clamping 101

Corner sections w/ turning vanes
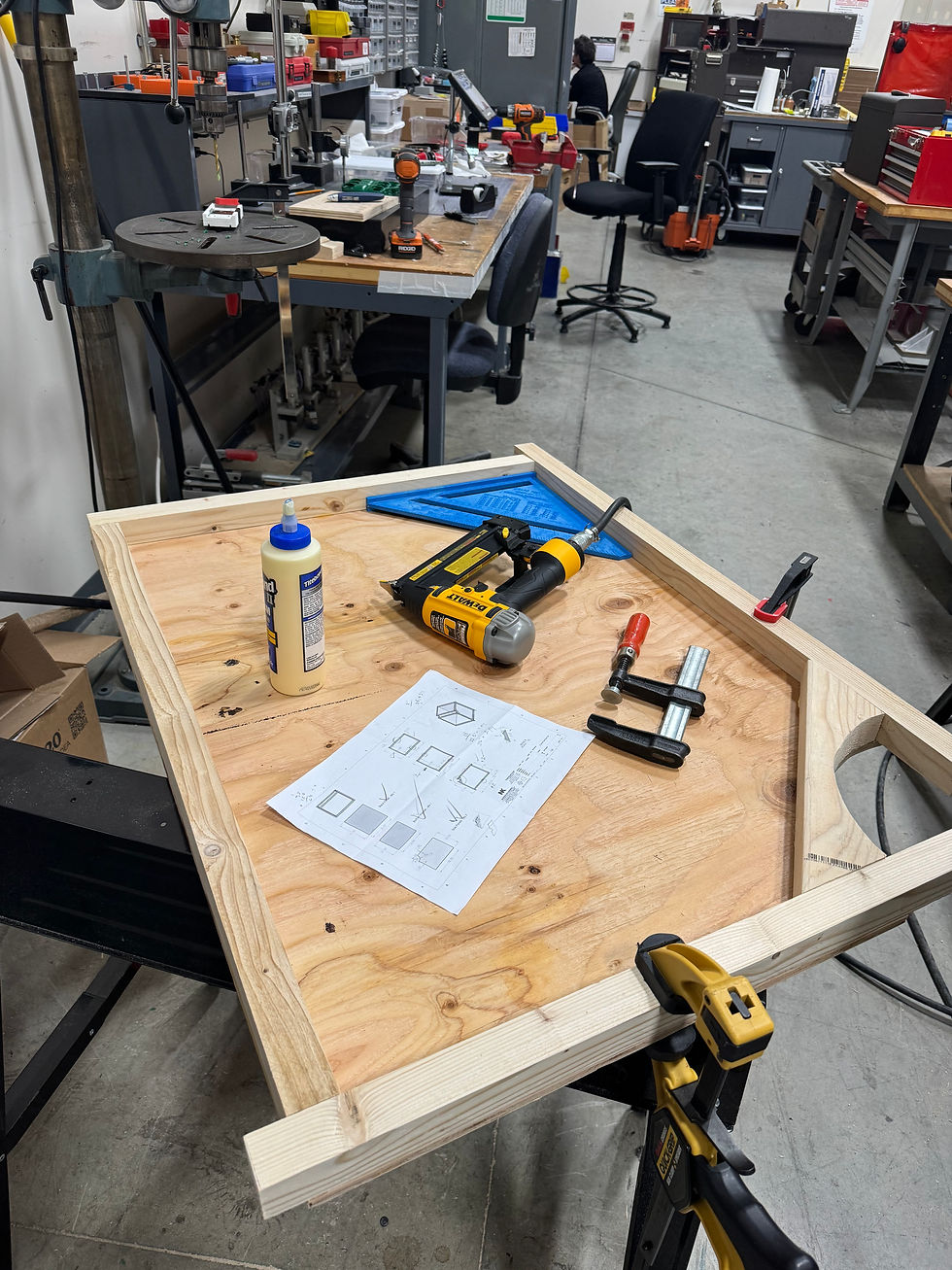
Squaring 101